For industrial facilities across Illinois and Iowa, rising heating costs pose a challenge. However, many businesses rely on air compressors for daily operations, and as much as 90% of the energy an air compressor uses is lost as heat. Instead of letting this valuable energy go to waste, heat recovery systems capture and repurpose it — helping companies reduce operating costs, improve sustainability, and maximize efficiency.
Delta Industries, Inc. installs and maintains industrial heat recovery systems to support cleaner, more energy-efficient businesses. These systems draw heat from the air at the top of a building or structure and pass it through the fresh air being filtered in from the outside.
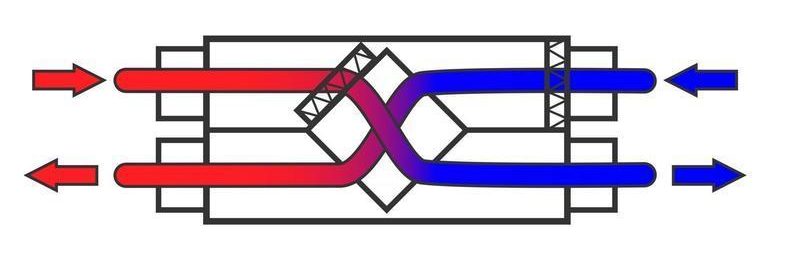
This process helps maintain and reduce your impact on the environment by using stale air or water that’s already warm to heat supply air. By reconstituting warm air, you relieve your boiler or heating system of some of its workload, reduce your energy consumption, and lessen your carbon footprint. A heat recovery system works independently of your standard heating system and can help your establishment save on costs related to heating your facility.
If you’re without a heat ventilation system utilizing an air-to-air heat exchanger to recover waste heat, supply highly filtered fresh air, and improve your indoor environment, Delta Industries is prepared to assist you with your air transfer needs. We’ll help you reclaim wasted energy and put it to work in your facility.
How Heat Recovery Works
To compress air, a compressor takes electrical energy and transforms it into mechanical energy. This process discharges a great deal of heat. At Delta Industries, we engineer industrial heat recovery systems to capture this waste heat and repurpose it for various other applications. Depending on your facility’s needs, there are two primary varieties of industrial waste heat recovery systems.
Air-Cooled Heat Recovery
This simple system harnesses waste heat from the cooling air of an air compressor and redirects it through ducts to heat office, workshop, or warehousing space within your facility. While this is a cost-effective option, an air-cooled heat recovery system is only applicable for delivering warm air.
Water-Cooled Heat Recovery
In a water-cooled heat recovery system, waste heat transfers to water via an aftercooler or oil cooler. The resulting heated water is then available for your hot-water supply or industrial process needs, pre-heating a boiler’s feedwater, or heating facility space. This versatile type of heat recovery system is known for its efficiency.
Key Considerations for Heat Recovery
By integrating a heat recovery system, you can reduce your heating expenses along with energy waste. To get the most out of your heat recovery system and meet your energy efficiency objectives, however, it’s important to keep the following factors in mind:
- System design. You should base the size of your system on your facility’s heating requirements and compressor. If you’re unsure of the appropriate sizing, check with our team and we can help design your system for optimized setup and performance.
- Compressor type. Heat recovery systems are beneficial for oil-injected and oil-free compressors alike. However, the implementation will vary based on your compressor type.
- Application. Your facility’s requirements for hot air and/or hot water will determine the best system for your unique needs.
- Return on investment (ROI). Depending on system efficiency and energy usage, most heat recovery systems will pay for themselves within one to three years.
- Regulatory compliance. Our Illinois and Iowa clients should consider local energy and heat-recovery regulations and incentives to ensure compliance and benefit from potential cost savings.
Common Applications for Heat Recovery Systems
Many industries benefit from integrating heat recovery solutions into their facilities for:
- Space heating. From offices to manufacturing floors, you can heat your facility spaces effectively with heat recovery systems while simultaneously lowering utility expenses.
- Water heating. Companies in such markets as chemical manufacturing and food processing use recovered heat to supply their hot water and reduce the amount they spend on energy.
- Industrial processes. For processes like pre-heating, curing, or drying materials, heat recovery supports applications requiring consistent heat inputs through thermal energy supply.
Key Benefits of Heat Recovery Systems
Heat recovery systems lend the above applications numerous benefits, such as:
- Prolonged equipment lifespan. The increased cooling efficiency that heat recovery systems make possible can extend the life cycle of your compressor.
- Energy efficiency. Particularly in energy-heavy applications, a heat recovery system can reclaim as much as 80% to 90% of your compressor’s input energy, significantly reducing waste heat.
- Lower carbon footprint. Repurposing waste heat helps lower your facility’s consumption of energy resources as well as reduce greenhouse gas emissions.
- Enhanced sustainability. Heat recovery also aligns with many companies’ corporate energy efficiency and sustainability initiatives.
- Decreased costs. Less dependence on external sources for delivering heat leads to lower energy bills.
Why Choose Delta Industries for Heat Recovery Systems in Illinois and Iowa?
Since 1987, Delta Industries has been helping industrial facilities in Illinois and Iowa harness the full potential of their compressed air systems. Our expertise in system design, installation, preventative maintenance, and repair ensures that our customers receive reliable, high-performance solutions tailored to their unique heat recovery needs.
With a focus on local, quality service, our team of technical specialists and system engineers is committed to improving efficiency, optimizing system performance, and reducing heating costs in our clients’ facilities. Contact Delta Industries today to learn more about our heat recovery system services, or request a quote to start maximizing your energy savings.