Delta Industries is committed to keeping you informed about how to care for your compressed air system, primarily how to service and maintain it during the hot summer days.
As summer gets closer, you can count on the temperature and humidity rising and taking a toll on your air compression system. Just like you, your compressed air system can get worn down in the heat of the summer months.
Summer weather will put pressure on your system, and you could see temperature alarms and dryer failures if you’re not properly maintaining it.
How the Heat of the Summer Months Affects Your Air Compressor?
It’s important to protect your air compressor since the heat can dramatically affect its operation.
Related: Rotary Screw vs Piston Air Compressors
A tired, worn system will not be operating like it needs to be in order to provide your facility with the compressed air required for daily production.
Lower Flow Rates
When the temperature is higher, as it can be in the summer months, the air becomes less dense. This means you will have less air coming through the intake of your system.
Increased Water Output
Higher temperatures mean more water in the air. Increased water vapor puts more pressure on your filtration and drying systems. The moisture can build up inside your system and, over time, cause corrosion and damage your equipment.
Increased Draining
Since your system is dealing with more water vapor, there will be an increase in system drainage. This will cause more wear and tear on your drainage system.
Rising Temperatures
Your air compressor creates a lot of heat on its own. Still, the higher air temperatures in summer will raise the temperature of your cooling water or air, thus further reducing your compressor’s efficiency. This can cause your system to overheat and shut down.
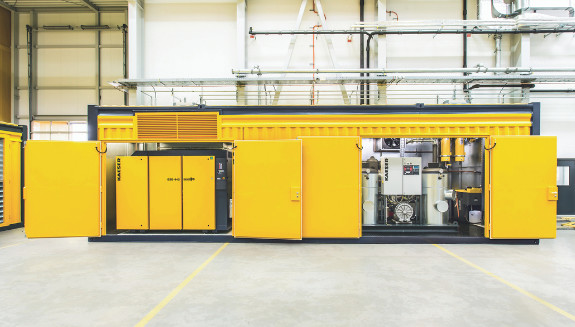
Related: Benefits of Oil-Free Air Compressors
10 Preventive and Maintenance Tips for Air Compressors During Summer
Delta Industries Inc. advises the following proactive preventive maintenance measures to keep your air systems running smoothly during summer to avoid unscheduled downtime in your facility and costly repairs.
1. Clean your Coolers
Clogged or blocked coolers will cause overheating and shut down your equipment. Keep your system functioning effectively by clearing away any dirt and debris in your coolers.
2. Change the Oil
High temperatures will shorten the life of the oil in your system and cause residue to build up in the internal oil passages. Your system will operate more efficiently if you change the oil before the heat of summer starts.
3. Change your Filters
Your system has to work harder when your filters are blocked, creating even more damaging heat. Make sure you start the summer with clean filters to get the best performance from your air compressor all season long.
4. Clean the Condensate Drain Traps
More condensate is created in the summer due to the high humidity. On a hot summer day, say 90°F with 80% relative humidity, a 50-hp compressor delivering 200 CFM of compressed air at 100°F squeezes about 2.1 gallons of water per hour from the atmospheric air! That is a lot, more than enough to fill a 40-gallon drum every day. Check your drains regularly and keep them clean to avoid any problems.
5. Check the Air Dryers
Your dryers need to be well ventilated, and the condenser needs to be clean so that there is a steady supply of clean, cool air or water. Prevent increased dew point and moisture in the air system by checking refrigerant gas levels, dryer condenser, drains, and filters.
Related: Benefits of On-Site Nitrogen Generators
6. Check Your Electrical Cabinet
Clean any dirt and dust from inside your electrical cabinet. Don’t forget to check your fans while you’re in there to make sure they are dust-free and running smoothly.
7. Check on the Ventilation of the Compressor Room
Avoid exposing your system to too much heat by adding ductwork to remove the excess exhaust from the room. Perform checks to keep the ductwork working correctly. The addition of fans or louvers to the room can also help lower the temperature. Air should be able to flow freely around your compressor and through the room.
8. Replace Worn Out Parts
Check over everything thoroughly at the beginning of the season. Replace any parts that are no longer performing correctly. One worn-out part can affect the quality of the entire system.
9. Increase Oil Checks
Oil levels should be checked more frequently and inspected for dirt and contamination during the summer.
10. Check for Oil Leaks
Excess heat can damage the integrity of small components, like gaskets and hoses. Check for leaks regularly and change these parts out as necessary.
Conclusion
Delta Industries Inc highly recommends summer service, which should include air filters, oil filters, oil, and cooler cleaning and temperature checks. To keep your air compressor running smoothly and avoid excess downtime at your plant or facility, it’s important not to neglect your system.
Take precautions ahead of time and be proactive to ensure your air system is ready for the summer.